Products center
Dedicated to the international trade business of processing and selling metal materials, building materials, and other products.

ABOUT US
Tianjin Zhongnan International
Tianjin Zhongnan International Trade Co., Ltd
Tianjin Zhongnan International Trade Co., Ltd is the branch office of Tangshan Hongyun Metal Products Co., Ltd., that are committed to the international trade business of selling and processing metal materials, building materials, and other steel products. The company is located in Tianjin Economic and Technological Development Zone, where is only 2 kilometers away from Tianjin Port , engaged in various types of steel materials, including steel section , coils, plates, pipes,tubes etc. Also providing various processing services such as hot rolling, cold rolling, cutting, precision machining, etc.
The company relies on strong funds and professional knowledge and adheres to the service philosophy of "honesty,trustworthiness, customer first", quality as the core, integrity as the foundation to build a stable supply channel and provide customers with high-quality products and services.

Honor

Cover an area

Annual total production
Production equipment
Dedicated to the international trade business of processing and selling metal materials, building materials, and other products.
Product advantages
Dedicated to the international trade business of processing and selling metal materials, building materials, and other products.

High quality
Ensure the quality of each batch of products produced and supplied.

Product customization
Customized services for special sizes, packaging, and customized signage.
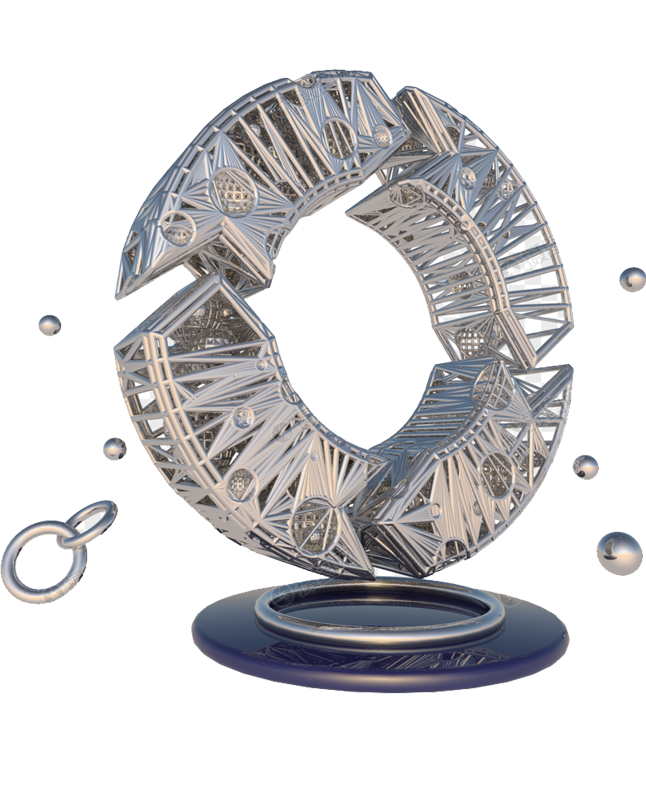

Large inventory
Provide a large inventory of standard sizes for your urgent order.

VIP reservation
Special discounts for large orders and long-term cooperative customers.
News center
Follow Zhongnan International and keep up with company trends in a timely manner

Reasons for Bubbles During Welding of Color Coated Plates
During the welding of color coated panels, bubbles may sometimes appear due to external factors, which can make the welding unstable and also affect the aesthetics. Therefore, we should try our best to avoid this situation when welding. What is the reason for this phenomenon? Only by finding the cause can we better solve it. Let's explain it to everyone below. If the surface of the weld seam on the color coated plate is not cleaned thoroughly, it is easy to cause the appearance of bubbles, such as the presence of oil stains, moisture, and other components. We can solve this problem by cleaning the surface of the weld to be welded. 2. Impurity of protective gas can also lead to the generation of bubbles, and 99.99% argon gas can be used to address this issue. If the welding wire end is exposed to air, bubbles may also occur. So, we need to keep the end of the welding wire under the protection of inert gas when welding the color coated plate. The three methods introduced above can effectively prevent the generation of bubbles during the welding of color coated plates. For bubbles that have already appeared, we can directly use an angle grinder to grind them off. In future practical operations, everyone can refer to the content introduced in this article, and I believe it can effectively solve your problem.

The benefits of using color coated boards
Because color coated boards strictly control each process in production and manufacturing, ensuring uniform quality in terms of appearance, durability, and process performance. The price of mass-produced color coated panels is cheap. Compared with the plating solution for finished products, the liquid components in building coatings have high water content, low consumption of organic chemical building coatings, and are cost-effective in economic development. The application of color coated boards can greatly simplify the production process and eliminate air pollution caused by organic chemistry solutions such as painting and baking. The commonly used types of architectural coatings include epoxy resin, polyester, silicone modified materials such as polyester, polyvinylidene fluoride, and polyurethane materials.
2021-11-09
Is the galvanized coil plate resistant to high temperature
The melting point of zinc is 419.5 ℃, and its chemical properties are vivid. In air at room temperature, a thin and dense basic zinc carbonate film is formed on the surface, which can prevent further oxidation. When the temperature reaches 225 ℃, zinc oxidizes violently and appears as white zinc oxide. After high-temperature barbecue, the anti-corrosion material on the surface of the galvanized sheet is oxidized, so the galvanized sheet cannot withstand high temperatures. The surface may change color when heated, or other protective substances on the surface may turn yellow after oxidation.
2021-11-09
The process flow of galvanized rolled sheet
1. Cold rolled steel plates are degreased through alkaline washing, washed with water, dried, and then annealed in a horizontal (vertical) heating furnace heated by a radiation tube. A certain amount of hydrogen gas is introduced into the furnace to reduce the atmosphere in the early stage. 2. Steel strips heated to a certain temperature are immersed in zinc solution under certain conditions for hot-dip galvanizing. 3. The size of zinc flakes is controlled by the composition of liquid zinc, and at the same time, forced cooling is used to control. Before the diffusion of zinc flakes begins, small zinc flake products are quenched using small zinc flake equipment to prevent the zinc liquid from continuing to spread, forming small zinc flakes. 4. After being cooled by hot dip galvanizing, the product undergoes surface finishing, and finally undergoes surface passivation treatment or direct production into color coated rolled sheets according to its purpose.